Engineers have spent decades trying to make factories smarter so that medicines and vaccines can reach patients faster. Today, robots, machine learning, artificial intelligence and other innovations are starting to give manufacturers a new way to deliver at speed and get ahead of disease.
At its most basic level, a manufacturing site makes a product to be delivered to a person who needs or wants it.
Sounds simple.
Yet when you are making potentially life-saving vaccines and medicines, this process involves hundreds of steps – and each one must be done 100% perfectly, every time. If not, the team must carry out a thorough investigation, which means delays and potentially having to discard a product and start over.
By harnessing the power of technology and data, smart manufacturing aims to optimise every step. This could include monitoring production processes in real-time, identifying ways to improve yields or predicting when equipment needs replacing. Ultimately, it allows biopharma companies to get vaccines and medicines of the highest quality standards to those who need them faster.
As Regis Simard, head of GSK’s global supply chain, says: “This is the beauty of science, technology and talented people working together to develop and deliver vaccines and medicines at scale and make a transformational impact on people’s lives.”
A report by global consultancy McKinsey & Company on the future of the biopharma industry found that facilities using a range of digital technology and advanced analytics saw a 25-40% increase in plant capacity and a 15-20% reduction in lead times.
“The biopharma industry is only at the start of the digitalisation and automation journey – and just a fraction of its potential has been delivered so far,” said Thibaut Dedeurwaerder, a partner at McKinsey & Company.
“We’re at a really exciting turning point – a key insight from our Global Lighthouse Network is that the impact of smart manufacturing becomes truly transformational when scaled at the intersection of technology, operations and strategic workforce planning.”
Getting smarter
Upper Merion is a GSK site in the US where investments in technology, digitalisation and automation are already starting to deliver real benefits – for the business and for patients.
A $120 million investment at the site in 2019 created a technologically advanced manufacturing hub that offers the flexibility and speed needed to make today’s complex specialty medicines. The strategic investment also laid the foundations for further advances in digitalisation and automation at the site.
Take for example digitalised scheduling. In simple terms, it’s a real-time modelling system that can tell people in operations what to do and in which order.
“It’s like a navigation system in your car – it gets you from A to B in the most efficient way,” explains site director Greg Naugle.
“It has been an absolute game-changer for us. It has removed bottlenecks in our operations, boosted efficiency and unlocked 10% more capacity.”
Unlocked capacity means more batches of medicines can be made per year and delivered to patients around the world.
The site also uses advanced analytics during production. The technology – a type of digital twin – detects early signs of a fault in the manufacturing process, allowing operators to intervene before an abnormality becomes an issue.
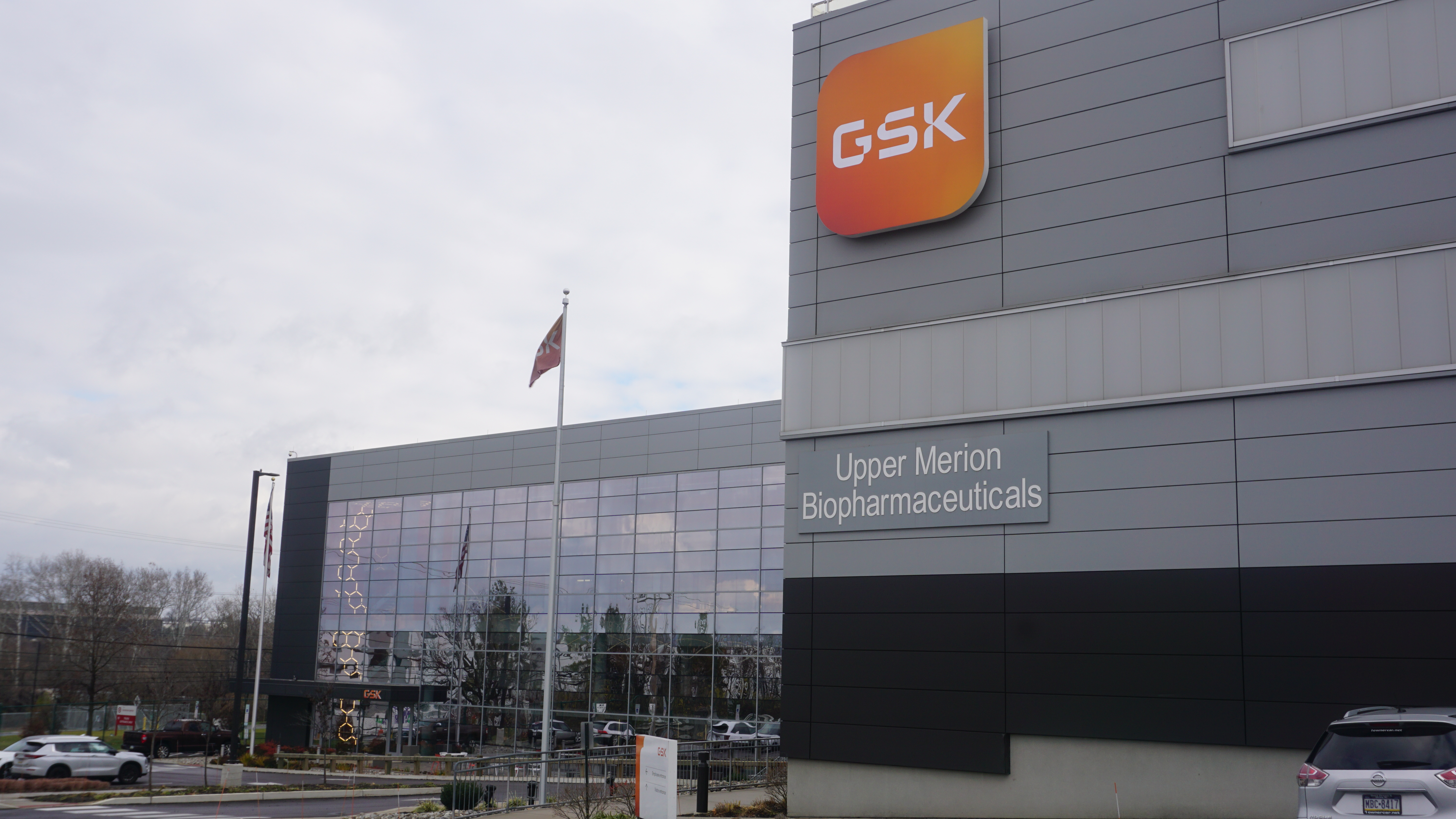
AI and robots
Data, analytics and insights from the different areas of the site all come into a high-tech digital control room with touch screens on the walls. It’s here that site personnel gain an end-to-end view of operations and better insight into how efficient their processes are. As a result, the site is reducing deviations and improving product yields – which, again, means getting treatments to those that need them faster.
Visit the analytical laboratory and you’ll find robots preparing samples for quality testing. There are many advantages to automation: it reduces the long-term ergonomic impact from excessive pipetting, reduces the number of laboratory investigations due to human errors, and improves the traceability of performance for data reviews and investigations.
Other sites across GSK’s network are also implementing technological advances to get ahead. For example, digital mathematical models are enabling teams to predict and improve the performance of vaccines and medicines during the manufacturing process using AI and machine learning capabilities.
Models can anticipate when equipment will need replacing, inform teams about how to best use stock, and what to change in the future to reduce the number of rejected products.
Due to digitalisation, sites are able to go paperless, increasing efficiency and accelerating the release of product batches.
How?
Electronic – rather than manual – batch records automatically collect data in real-time throughout the manufacturing process, eliminate calculation errors and create an enforced workflow to ensure no steps are missed.
This means people only have to review the exceptions or anomalies when they occur, which can reduce the number of pages to be reviewed from 100s per batch to about 20 or 30, saving one of the most essential resources out there – time.
“Technology is at the core of strategy to drive innovation in how we discover, develop and bring medicines and vaccines to patients. It is exciting to see the emerging results from the successful integration of science, advanced technology and great talent,” said Shobie Ramakrishnan, GSK’s Chief Digital and Technology Officer.
People power
There’s no doubt that technology is changing the workplace, but it’s changing the type of work that people do rather than replacing people.
Robotics will increasingly be used for more repetitive processes, leaving higher skilled jobs open. Automation has a role for improving ergonomics, too. Instead of having people dragging boxes and pallets around the floor, automated guided vehicles (AGVs) can do the heavy lifting. Similarly, smart systems are capable of sifting through and verifying data more efficiently and effectively than humans.
However, people are still needed to understand data-based decisions.
“It’s a state-of-the-art facility that we have here in Upper Merion,” Naugle says. “Alongside our investments in technology, we’re also investing in people.
“There’s a whole new generation of STEM [Science, Technology, Engineering and Maths] students who want to work in a digitally enabled environment.
“I’m proud of what we’ve already achieved and excited about the further advances we can make.”